Rotomolding
Procesos > ► Moldeo
Moldeo rotacional
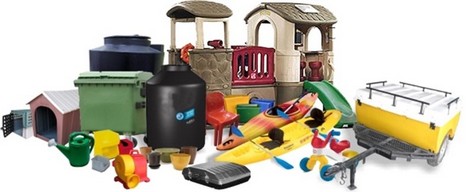
Polvo plástico para rotomolding
La forma de polvo plástico que se usa generalmente tiene un tamaño de partícula de malla 35 (74 a 2000 am). El tamaño de partícula de los polvos generalmente se cuantifica en términos del tamaño de malla. Esto se relaciona con el número de aberturas de malla por pulgada en el tamiz utilizado para clasificar el polvo que se define en los estándares de tamaño de malla de la industria. Algunos plásticos de alto flujo, como el nailon, se han utilizado en forma de gránulos pequeños. El acetato de vinilo de etileno y los PE también se utilizan en aplicaciones especializadas, como PVC, PC, poliéster TP, nailon y PP. Los plastisoles de vinilo RM producen diferentes productos, como pelotas de playa, animales flotantes y juguetes, así como productos industriales. El plástico líquido o en polvo usado en este método fluye libremente hacia las esquinas u otras embuticiones profundas al girar el molde y luego se fusiona con el calor que pasa a través de la pared del molde. Los plásticos usados en RM generalmente son más caros que los plásticos granulados usados en muchos otros procesos porque deben ser pulverizados más fina y uniformemente.
Ventajas rotomolding
Existe un grado de compensación sobre el plástico utilizado en RM. El proceso genera niveles bajos o nulos de material triturado o chatarra, incluso cuando funciona de manera ineficiente. Con moldes correctamente diseñados, los productos pueden no tener rebabas. El moldeo de dos o más tipos diferentes de plásticos en un solo producto puede lograrse para combinar sus propiedades específicas y/o un producto de mejor desempeño o de menor costo. Este proceso, llamado corotación, es similar a la coinyección o coextrusión en términos del rendimiento del producto diseñado. Si bien RM tiene muchas ventajas, como costos de molde bajos, molduras sin costuras y sin tensión, distribución controlada del espesor de la pared, etc., se caracteriza por sin cizallamiento durante la conformación y velocidades de enfriamiento lentas. Estos dos factores conducen a características estructurales únicas en los productos RM. La ausencia de cizallamiento no fomenta una buena mezcla de aditivos tales como pigmentos, y el enfriamiento lento promueve un gran crecimiento esferulítico. Además, los tiempos de ciclo más largos y la presencia de oxígeno en la superficie libre interior de las piezas moldeadas significa que los procesos de degradación pueden iniciarse muy rápidamente si no se utilizan las condiciones de moldeo correctas. RM tiene características que contribuyen a la microestructura del producto de plástico moldeado. Con velocidades lentas, la masa fundida tiene un cizallamiento bajo que desarrolla texturas libres de orientación. Sin embargo evita la dispersión de aditivos como pigmentos. Si el calentamiento del plástico es demasiado excesivo, su degradación puede ocurrir en la superficie libre interior, lo que hace que las esferulitas que crecen libremente en esa superficie sean reemplazadas por una textura no esferulítica o transcristalina, según el grado de degradación (las esferulitas son agregados redondeados de laminillas radiantes) cristales). La microestructura plástica en masa, y también en la capa superficial interna, tiene una gran influencia en las propiedades mecánicas del material moldeado. El polietileno (PE) y el polipropileno (PP) regulares y reticulados tienen un efecto o influyen en el proceso de RM, como la temperatura de moldeo, las condiciones de molienda y mezcla, el tipo y el nivel de aditivo (pigmento, antioxidante, etc.), el material de construcción del molde. y ambiente interior. Como ejemplo, el uso de mayores cantidades de antioxidante en el plástico, o el uso de una atmósfera inerte, retrasa la degradación pero no la previene. La rigidez o flexibilidad del producto moldeado está controlada por la formulación del plástico utilizado, por el espesor de la pared y por la forma. Con el aumento de la temperatura de fusión del LDPE, se produce una disminución de la resistencia química, la ductilidad, la resistencia al impacto, la resistencia a la tracción, el módulo de elasticidad y la resistencia a la intemperie. Los ejemplos de las ventajas del producto incluyen sin costuras, sin estrés, tiempo de entrega corto para la fabricación de moldes, una o más cavidades en un molde pueden procesar plásticos iguales o diferentes, corotación de plásticos, incluido el plástico reciclado, y espuma plástica. Los diferentes polvos de moldeo que tienen diferentes temperaturas de ablandamiento/fusión se pueden moldear simultáneamente o por separado, según las condiciones de procesamiento y los requisitos del producto final.
Tamaño
El tamaño físico puede eliminar algunos métodos de fabricación de herramientas. La mayoría de los moldes grandes se fabrican con láminas de metal, aunque las piezas de fundición grandes, como las de 18 pies. (5,5 m) los kayaks se pueden producir en un solo vertido. La fundición de aluminio a menudo se limita al tamaño de las piezas de fundición individuales por la capacidad del horno utilizado, pero se pueden fabricar moldes más grandes combinando varias piezas de fundición y soldando o atornillándolas juntas. También debe tenerse en cuenta el coste de fabricación de un patrón muy grande para fundición.
Complejidad de la forma
La geometría de la pieza también afectará la decisión. Las características, como radios de esquina, insertos, orificios, roscas, etc., pueden afectar la elección de los materiales del molde y también afectar cómo se debe montar una pieza o cómo se construye una línea de partición. Las líneas de partición complejas, que requieren más de una pieza de molde y no pueden encajar en un solo plano, complicarán la fabricación del molde. Los insertos de molde (núcleos, etc.) que se quitan cada vez que se abre el molde afectarán la construcción del molde al introducir puntos de desgaste. Se prefieren los insertos fijos que deban intercambiarse con menos frecuencia. Los moldes detallados que requieren un alto grado de precisión favorecerán el mecanizado, el electroformado o la fundición sobre los métodos fabricados. El grabado químico no es común, pero se puede usar en moldes de acero para crear detalles y patrones finos en la superficie.
Cantidad de moldes
Cuando se requieren múltiples moldes, se debe tener en cuenta el nivel de repetibilidad que se puede lograr al elegir un método de fabricación de moldes. Los moldes de chapa metálica han mejorado considerablemente, pero la fundición, el electroformado o el mecanizado ofrecen una precisión mejor y más repetible. Los moldes de fundición repetida tienen un costo más bajo debido al hecho de que se puede usar el mismo patrón maestro. Las corridas de producción de alto volumen que pueden usar moldes de acero o aluminio a menudo se fabricarán en aluminio fundido debido a la repetibilidad. Las corridas de producción de menor volumen a menudo aprovecharán la capacidad de utilizar herramientas de chapa metálica de menor costo o incluso herramientas compuestas para producir lotes pequeños; a medida que aumentan los volúmenes, el proyecto se puede convertir en moldes de fundición.
Aspecto del producto
El acabado de la superficie requerido para una pieza también puede determinar qué proceso se utiliza para producir un molde. Se pueden agregar algunos acabados y detalles de la superficie durante la fundición o la fabricación; otros se pueden agregar una vez terminado el molde (granallado, grabado). Los moldes de aluminio o electroformados pueden producir una gama más amplia de acabados superficiales que los moldes de láminas de metal; se pueden incorporar fácilmente fundiciones intrincadas y superficies grabadas al patrón. La chapa se puede texturizar ligeramente después de la formación e incluso se pueden usar placas estampadas y grabado químico para producir acabados más complejos. Las piezas que requieran un acabado muy pulido favorecerán los moldes mecanizados de aluminio o niquelado. El aluminio fundido y el acero se pueden bruñir para obtener un acabado pulido, pero no un acabado de espejo. Los diseñadores deben tener en cuenta que los acabados pulidos requieren muchas horas de trabajo manual en un molde y pueden aumentar considerablemente el costo de un molde. Además, los acabados en los núcleos deben considerarse con cuidado: las superficies muy pulidas pueden crear un vacío, mientras que las texturas rugosas pueden proporcionar suficiente agarre para bloquear una pieza en el molde.
Espesor de la pared
El moldeo rotacional tiene la ventaja de que el espesor de la pared se puede variar después de fabricar el molde, sin embargo, es mejor tener en cuenta un espesor de pared nominal cuando se diseña la pieza. Las piezas se forman contra la superficie exterior de la pieza (superficie interior del molde) sin núcleos, lo que permite variar fácilmente el grosor de la pared. Cambios similares en otros procesos significarían modificaciones sustanciales del molde. Sin embargo, debe recordarse que las piezas más gruesas tienden a encogerse más que las piezas más delgadas y, por lo tanto, pueden causar problemas de ajuste. Además, las piezas más gruesas requerirán ciclos de enfriamiento y horno más prolongados. La distribución del espesor de la pared se ve afectada por las tasas de transferencia de calor, la relación y las tasas de rotación del molde, el espesor y el material de la pared del molde, las características del polvo y el agente de desmoldeo. Los principales factores son la transferencia de calor y la relación de rotación. Mantener un espesor de pared uniforme es muy importante, ya que ayuda a velocidades de enfriamiento uniformes y reduce la posibilidad de deformaciones. A pesar del hecho de que la superficie interna de la pieza se forma libremente en el moldeo rotacional, la distribución del material dentro de una pieza moldeada será generalmente bastante uniforme. La variación del espesor de la pared se calcula normalmente en ± 20% para la mayoría de las aplicaciones comerciales. Sin embargo, un ajuste cuidadoso del molde y los parámetros de moldeo puede alcanzar ± 10% (con un posible aumento correspondiente en los costos). Al especificar el grosor de la pared en una pieza moldeada por rotación, es mejor establecer un grosor de pared nominal junto con un grosor mínimo.
Ángulos de tiro
Es posible producir piezas con cero tiro en el moldeo rotacional ya que el material se contrae y se aleja de la pared del molde durante el enfriamiento. Sin embargo, en la mayoría de los casos, es mejor tener un borrador en una pieza para ayudar a sacarla del molde. Para una pieza hueca grande, es posible que no se necesite un desmoldeo en la superficie exterior, pero si un grado de desmoldeo no afectará la función de la parte, entonces se debe utilizar el desmoldeo. El ángulo real dependerá del material que se utilice. Los materiales con altos niveles de contracción (cristalinos) como el polietileno y el nailon se alejarán de la cavidad mucho más que los materiales de bajo nivel de contracción (amorfos) como el policarbonato. Además, los materiales como el nailon y el policarbonato son mucho más rígidos que el polietileno y, por lo tanto, requieren más corrientes de aire para facilitar su extracción.
Tolerancias
Las estolerancias de contracción para piezas rotomoldeadas generalmente se dan como un porcentaje de las dimensiones o un valor de pulgada por pulgada (cm por cm). El diseñador debe esforzarse por utilizar la tolerancia más amplia posible que pueda ser tolerada por la aplicación final. Sobreespecificar las tolerancias conduce inevitablemente a mayores costos y reelaboración de moldes o piezas. Dos variables de diseño tienen un efecto importante en las dimensiones finales de la pieza. El primero es la calidad y precisión del patrón; esto a menudo se minimiza mediante el uso de patrones mecanizados CNC o moldes mecanizados CNC. La segunda variable es el valor de contracción que se usa para hacer un patrón. La determinación de este valor requiere una comprensión del material que se utiliza, el tamaño y el grosor de la pieza, la complejidad del diseño de la pieza y el efecto de las variables de procesamiento. Puede ser difícil anticipar la contracción real de la pieza, ya que las variables en el proceso de moldeo, como el color, la distribución del espesor de la pared, el agente de liberación y los ciclos de enfriamiento, pueden variar. Las piezas grandes suelen tener una mayor contracción y, por lo tanto, serán más difíciles de mantener con tolerancias estrechas que las piezas pequeñas. Las piezas más gruesas también variarán más debido a niveles más altos de contracción que las piezas más delgadas.
Máquina rotomolding
La construcción de máquinas requiere diferentes requisitos según el tipo de producto a moldear. Existen el lote y los tipos de carrusel más comunes. El tipo de lote se opera manualmente al entrar en un horno seguido de la estación de enfriamiento. El tipo carrusel con básicamente sus tres o cuatro estaciones incluye una estación de carga, calentamiento, enfriamiento y retiro del producto. Se utilizan tres brazos en voladizo con una separación de 120° en una torreta central de modo que cuando un brazo con un molde sale de una estación, otro lo sigue hacia esa estación. Todas las operaciones funcionan automáticamente. Las máquinas de cuatro brazos pueden proporcionar un segundo horno, enfriador o estación de carga, según cuál consuma más tiempo, de modo que se pueda reducir el tiempo del ciclo. Hay rotación de doble eje, carrusel, lanzadera, bivalva, máquinas de rock and roll, etc. Estos diseños son similares a otros sistemas de moldeo en los que se pueden usar múltiples moldes para acelerar o incluso simplificar la producción. RM de doble eje utiliza dos plataformas para sujetar moldes. Los tipos de carrusel pueden tener de tres a seis brazos para montar moldes.
Proceso para rotomolding
Los moldes huecos se llenan con plástico en polvo y se fijan a radios en forma de tubo que se extienden desde un cubo central. Los moldes giran sobre dos ejes separados a la vez. El cubo hace pivotar todo el molde en una sala de horno cerrada que hace que el polvo se derrita y se adhiera al interior de los moldes. Con los moldes aún girando lentamente, entra en una sala de enfriamiento donde el agua rociada hace que el plástico se endurezca y se convierta en una parte hueca.
- La maquinaria utilizada es relativamente simple comparada con otros procesos de transformación (ejemplos: inyección, extrusión, etc.)
- El rotomoldeo se puede clasificar por las diferentes formas de calentamiento utilizadas:
- Por flama abierta
- En hornos cerrados
Elementos y características del molde
Muchos de los componentes básicos de los moldes son similares independientemente del proceso de fabricación elegido. Cada molde requiere una placa de montaje (1) para poder fijarlo a la máquina, un marco para soportar la cavidad del molde (2), postes para conectar al molde (3) (a menudo con resorte), una brida de línea de separación (4 ), la propia cavidad (5), los mecanismos de sujeción o atornillado (6), los puntos de palanca (7), un respiradero (8) y los puntos de elevación (9). Se pueden agregar insertos, núcleos extraíbles y otros dispositivos auxiliares según sea necesario.
1. Placa de montaje
2. Estructura
3. Postes de soporte
4. Línea de separación
5. Cavidad del molde
6. Mecanismos de sujeción
7. Puntos de palanca
8. Ventilación
9. Puntos de elevación
10. Inserciones y núcleos: secciones del molde
11. Puertos de llenado
12. Mecanismos de bisagra
13. Guías de rodillos
14. Caja de distribución
15. Amplificadores de flujo de aire (generadores de vórtice)
Rotomoldeo por flama abierta
En el rotomoldeo por flama abierta el calentamiento se realiza por mecheros que rodean al molde al “aire libre”. Lo cual provoca que la mayor parte del calor se disipe al medio ambiente. Por otro lado estas maquinas no pueden hacer giros biaxiales al mismo tiempo. Están sometidas a realizar giros de 360 grados y el siguiente giro lo tienen en aproximadamente 45 grados. Razones por la cual no se pueden realizar piezas complejas por el método de llama abierta. En el método por horneado el molde es introducido en un horno cerrado en donde se hace girar. Este último método permite un mejor control de los parámetros de temperatura.
Hornos los moldes
En estos hornos los moldes son introducidos en el horno alternativamente en un eje lineal. Mientras uno esta en etapa de calentamiento, el otro esta en etapa de enfriado y desmolde por flujo de aire proveniente de ventiladores.
Horno basculante
En el horno basculante o “rock and roll”, el molde gira el eje longitudinal mientras se balancea, sin completar el giro, sobre su eje lateral. Por lo general, se trata de moldes para obtención de piezas de un largo considerable como el caso de canoas de seis o más metros.
Estacion simple (Clam shell)
Este método cuenta con un único brazo portador de un único molde, que se introduce en un horno tipo almeja o “clam shell” para el calentamiento del material. También existen equipos de rotomoldeo que mediante uno o mas brazos introducen el molde en un horno para la fusión del material, siendo el mismo brazo el que lo introduce en una estación de enfriamiento. Las más comunes son las siguientes.
Moldeo por inyección vs moldeo rotacional: ¿Qué proceso gana?
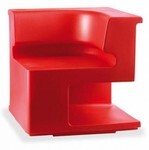
¿Por qué algunos fabricantes producen productos de moldes de inyección?
Ventajas
- Bajos costos de herramientas
- Piezas tan pequeñas como pelotas de golf en un tanque agrícola de 22,500 galones
- Prototipos económicos
- Esquinas exteriores resistentes en piezas prácticamente libres de estrés
- Acabado de la pieza de mate a alto brillo
- Procesamiento simultáneo de diferentes piezas
- Cambios rápidos de molde
- Posibilidad de moldear en inserciones metálicas
- Moldeado con gráficos multicolores
- Moldeado multicapa para resistencia química o resistencia.
- Moldeado de piezas de doble pared para mayor rigidez
- Posibilidad de cortes menores
- Uso virtual 100% de material (sin desperdicio)
Desventajas
- Los tiempos de ciclo lentos significan altos precios por pieza. Los tiempos de ciclo promedio son alrededor de 40-45 minutos